If you’re looking for an actual tutorial on how to make a cider press, this probably isn’t a good place to start. If however you want to read my ranting, then hi! welcome!
I first made cider a couple of years ago…used my garden shredder, a borrowed press, a big fermenting vessel, and lots of demijohns. I ended up with some lovely cider, and lots of vinegar (not that I’m complaining, it’s come in very useful). So this time it will be demijohn only, cos I can’t get an airlock for the huge vessel, and I am sure that is what caused the vinegarification. Well, that and forgetting to check on the fermentation regularly and then tighten up the lid when it was done. And also probably by not making enough juice and leaving a huge headspace in the vessel. It was stupidly heavy and got in the way in the kitchen anyway, demijohns are easier, and we can try different apple blends in each.
Sadly, the person who I borrowed the press from remembered that I had it, and asked for it back. We were toying of other juice pressing methods involving colanders and heavy weights, lots of wastage and lots of mess. In the end I decided to suck it up and just make my own. I decided against one with a bucket, mostly because that involves way too much precision cutting and screwing and finding suitable bits of metal. I also decided to use an old car jack rather than the huge monster screw, cos the screws are £25+, and you need the other bits of hardware to go with it too. For this press I think I spent £8 or so on timber, £7-something on coach bolts, of which I used 8 from a bag of 50, and £2.36 on silicone sealant (I have no idea why that is the only thing i remembered the exact price of).
I bought 2 lengths of 3×2 timber. Well, it would be 3×2 in the olden days, but it was actually 75mmx47mmx2400mm. I decided to get it from B&Q rather than the local (well, not so local, but cheap) wood yard, cos B&Q have a cutting service proudly announced on their website and in their shop. I took my lengths of wood to the cutting guy, and he told me ‘oh, no, we don’t cut lengths of timber, I can only cut board’, and showed me his awesome board cutting machine. Now, they sell about 20 different power saws that would do the job adequately, but apparently are unable to set one up in the shop to help me. Bastards. I mean, I know their ‘yay we are awesome we cut your timber!!!’ sign does have ‘terms and conditions apply’ in teeny tiny lettering on their website and in their shop, but I never once considered it might translate as ‘well, actually, we don’t cut your timber’. I did consider trying to kill the cutting man with my eyes, but then figured it wasn’t actually his fault, and he was a very nice man, so I saved my energy and went to pay, and had a battle with the self service checkout because I REALLY didn’t want to have to move these ridiculously long bits of wood into the bagging area to prove I wasn’t trying to steal them, or whatever the fuck their stupid reasoning behind that function is.
I maneuvered the ridiculous lengths of wood into my car, and they only needed to poke out the window a couple of inches, so it wasn’t too traumatic, and went to screwfix to embarrass myself. I was all organised with the catalogue number of the coach bolts I wanted ready, and it all went well until the cute guy at the counter asked if I wanted anything else. In my sulk at b&q i said ‘well I’d kinda like an electric mitre saw, but i don’t really neeeed one, and i can’t afford it, and i can borrow one anyway if i want to drive for 10 minutes’. So we talked about saws a bit, then he asked if i wanted anything else, and I said no, paid, and he went to get my bolts. Just as he walked away to the storeroom I was like ‘oh no wait I do want something else!!!’. I forgot I wanted silicone sealant both for the press and to fix the chicken’s water trough. So I am sure I was a very annoying customer.
Armed with my wood and bolts and silicone, I went home and called my dad to see if I could borrow his saw and the squeezy gun thing you use with the silicone. He said yes, AND said he’d bring them over and help….score!
So while I was waiting I laid out my stuff.
This is a picture of some wood. I think the jack decided to sneak into the photo too. I don’t exactly know WHY I have two jacks, given that I only have one car, but having a spare is useful, because I know if I used the car one I’d forget to put it back, and then I’d get a flat the next day and then I’d be one of those annoying women who calls the RAC out because she is too incompetent to change a wheel by herself.

I got out lots of tools.

Then my assistant arrived, woohoo!
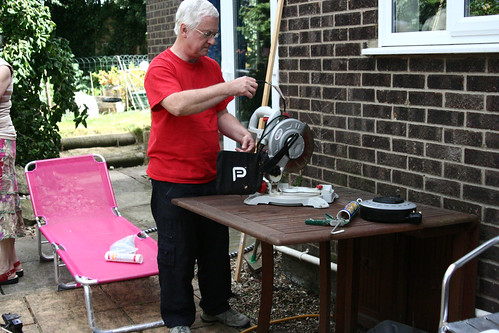
We cut each length of timber into 4 60cm lengths. Well, we cut them into 4 equal bits, because of course it didn’t actually measure what it was supposed to, but I wanted to do this the easiest way possible, so as long as they were equal, I didn’t care. If you want to make an exact copy of my cider press, make sure your pieces are 597.354mm long.

Then we needed to drill some holes for the bolts. The plan was to mark the first 4 sets of two holes, drill them, then use those holes to mark up for the second set, then repeat for the 3rd set. I wouldn’t even want to attempt this with a hand drill, as I’m pretty sure I’m incapable of drilling in a straight line, so we went to the garage to use the pillar drill. Then I realised i had no fucking clue where the chuck key was. The two drills I use most have keyless chucks, so it’s not something that I think about on a regular basis. After looking in all my toolboxes, shelves and drawers, I still had no idea where the chuck key was, but I decided my superhuman strength would be enough to hold the bit in place, seeing as the wood would be eeeasy to drill. And it was, and suprisingly my plan of marking and everything all worked out, and all the holes lined up and it was awesome. I did need to hit it with a rubber mallet a few times, but that was ok, and just added to the fun.
This is what we returned from the garage with.

At that point I decided a well fed workforce is a happy workforce, so we stopped for sandwiches and beer, kindly made by my mum in a break from her quality control (making sure the holes went all the way through) and HR (making sure dad and I didn’t argue or mess around too much) duties.
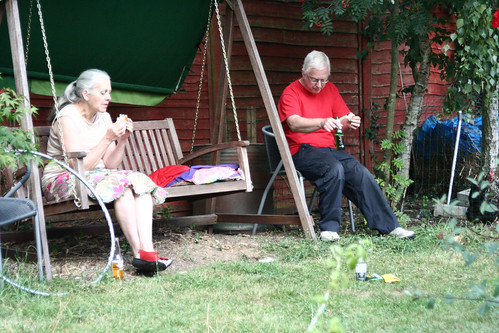
Then I drilled some holes in the legs and screwed them on. I didn’t bother with bolts for this bit cos it would have been a pain in the ass fitting them around the other bolts, and would have probably weakened the wood with all those holes anyway. Plus the legs aren’t under much force, they just stop it falling over.

At some point here I moved my camera to stop it getting dust in, so I forgot to take more pics for a while, but what we did was:
Located an offcut of kitchen worktop in my garage. It has been there for 12 years, but I KNEW it would come in useful at some point! Cut this so it rests on the bottom crossbeam and on the legs for extra support. Cut some bits of other wood (1×2″ maybe? I dunno, whatever, that came out of my stash in the garage too), and screwed them together into a square frame with a hole drilled into the front as low as i could get it without splitting the wood. Then we glued this frame onto the bit of worktop, and shoved a bit of syphon tubing into the hole.
And that brings us to the almost-finished product.
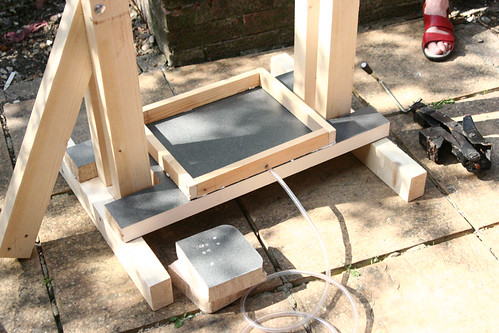
Now all it needs is a coat of varnish on the bare wood parts, and some sealer around the worktop/rim join. Then I need to grab a couple of bits of waste wood/worktop to use between the jack and the frame/apples to get even pressure, and it’ll all be in working order!