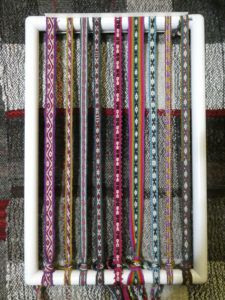
This month a group of more than 50 of us are taking part in Abby Franquemont’s first online Andean backstrap weaving class through Franquemont University, her online teaching platform. She has been teaching this style of weaving since she was a child, for more than 40 years, but has only recently figured out a way to translate showing this very hands-on skill via online classes while maintaining cultural context.
The biggest initial hurdle was supplying the warps. Having a properly wound warp of the correct material is essential to your success in this sort of weaving, and when taught in Peru beginners learn to operate their looms and weave basic patterns long before they learn to wind their own warps. Being taught in the traditional method, we had to do this too. So, for these classes to succeed, we all needed to have our warps wound by an experienced weaver. The Young Weavers Group at Away Riqcharicheq in Chinchero took on this mammoth task for us, and wound 300 beginner warps, which were shipped in bulk to the US, UK, and EU to then be sent on to their final homes.
We are now at the stage of the of learning where we can operate our looms, we can weave one or two basic patterns, can tie our illawas, and are ready to learn how to wind our own warps. As I am one of Abby’s adjunct professors, I got to start this course a little early so I’m far enough ahead of my classmates to be able to answer questions as they arise. This is good for my learning too, as part of learning to weave in this style is learning to teach those who aren’t as advanced as you; children teach younger children, there are no formal classroom lessons with adult teachers.
One of the questions that has come up repeatedly is ‘what is the best yarn to make my warps from?’ The answer is simple, and doesn’t change. Khaitu. Andean weaving yarn handspun with the characteristics needed, which pretty much boil down to twist. A lot of twist. High singles twist, and incredibly unbelievably (to a western spinner) high ply twist, far past the point of twist stasis. The question that follows is normally ‘what if I can’t spin my own yarn, what yarn can I buy that will do the job?’. The answer is none. They are all shit. There are no commercially available yarns that have enough twist to work. However, all is not lost. While you can’t go out and buy yarn and immediately wind a warp, there are yarns that you can buy and add extra twist to on a spindle, wheel, or e-spinner, which will make adequate warps. Not good warps, but adequate.
I’ve been doing some experimenting so you don’t have to. Here are my results so far. First come the yarns with no added twist, as they were bought. Now I knew these wouldn’t work before I tried them, I trust Abby, but one of the most oft-uttered phrases in her classes are ‘what happened when you tried?’. Well, I tried so you don’t have to.
Knitpicks palette.
This was far stretchier and more elastic than the handspun yarn I’ve been using thus far, and it was surprisingly hard to wind the warp maintaining even tension and keeping the knots lined up. After winding, I set up to tie my illawa, and could already see and feel the yarn beginning to fuzz and shed.
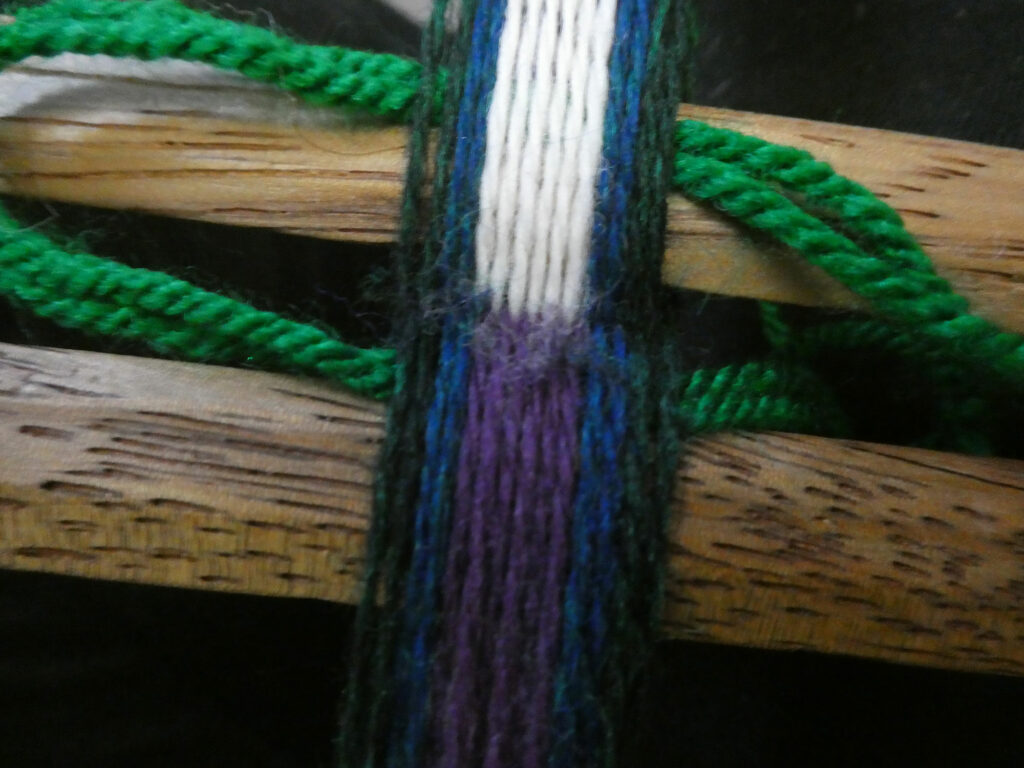
As I started weaving, each pick became harder as there was more buildup of lint on the illawa, between the khallwa, and pretty much all over the part of the warp I was using, making getting a clean shed a challenge, and meaning I had to strum the warp and pick bits off that were getting in the way. With every beat I was pushing excess fluff into the pattern, obscuring it and making it look messy.
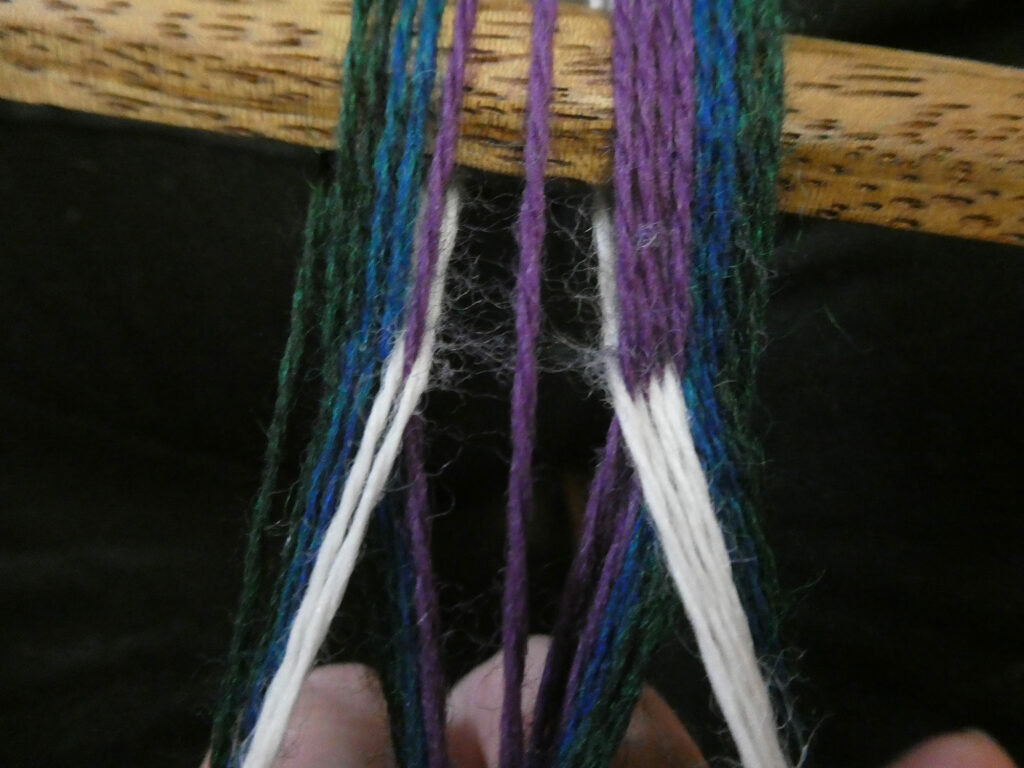
I gave up after this much as clearing the shed each time was getting to be too much work.
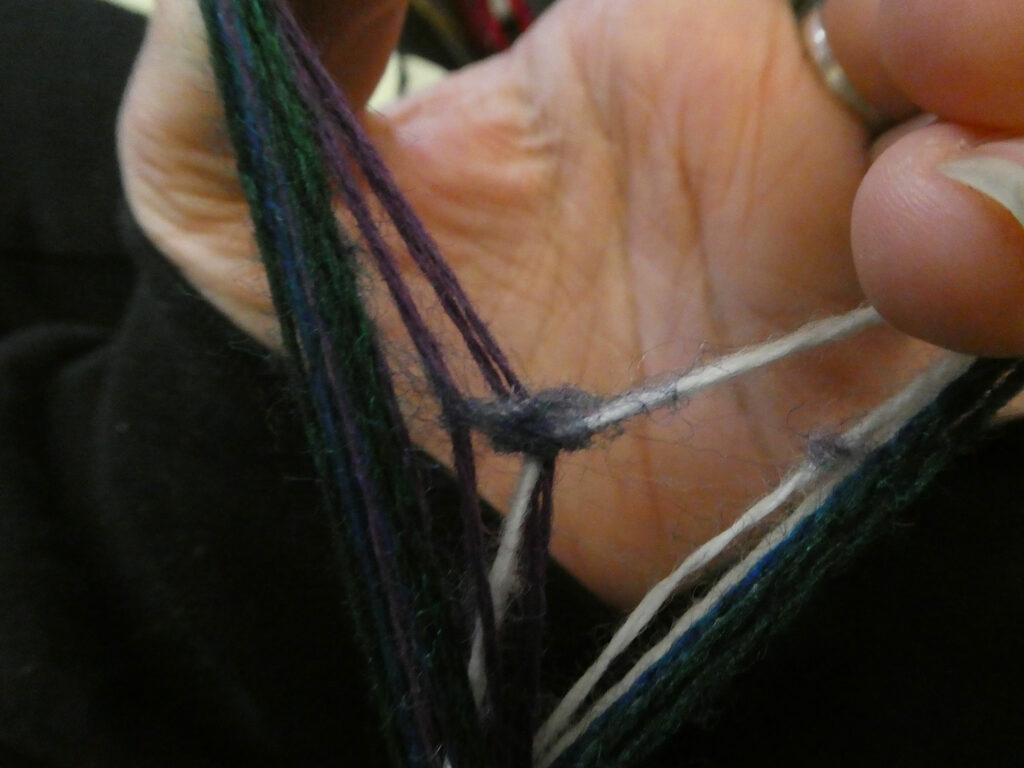
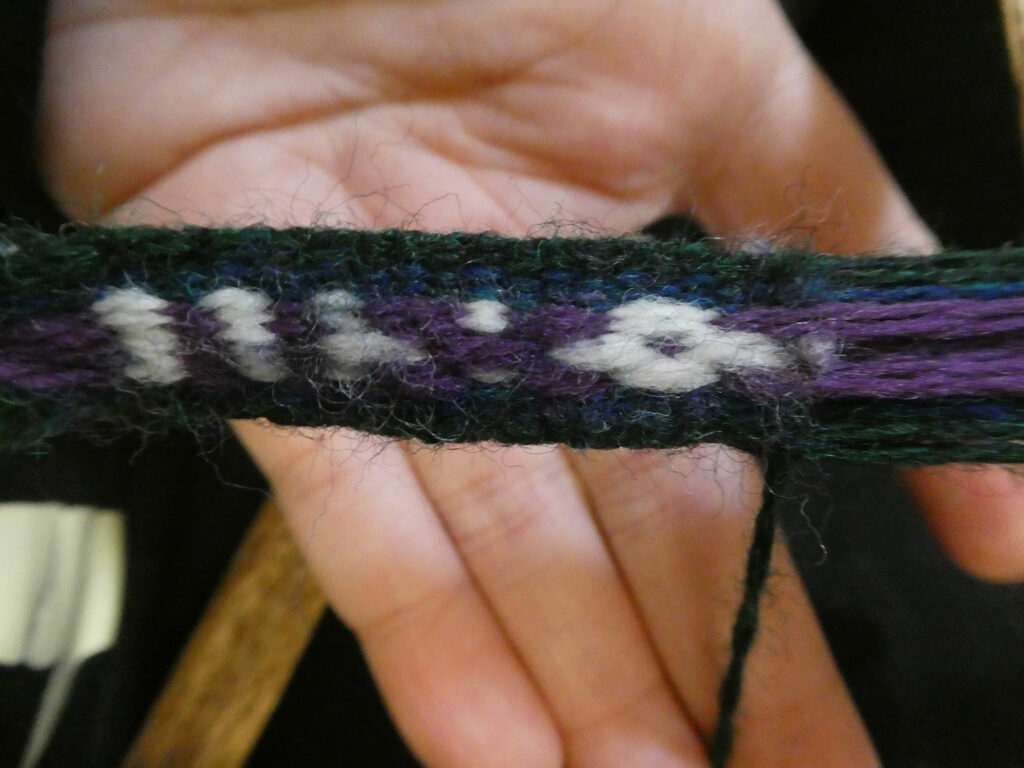
Rating: Terrible, 1/10. At least it didn’t break.
Sock yarn
This was from my stash of sock yarn leftovers, so is from a variety of brands. I believe it was all 20-25% nylon with the rest being wool, some merino, some not, spun with a moderately high twist for commercial knitting yarn.
While winding the warp this yarn was also noticeably more elastic that I was used to, although not as bad as the knitpicks.
I managed to get the illawa tied and the first few picks woven without any issue, although it was already apparent that the threads settled into each other in the way the proper yarn doesn’t, making the patterns less distinct.
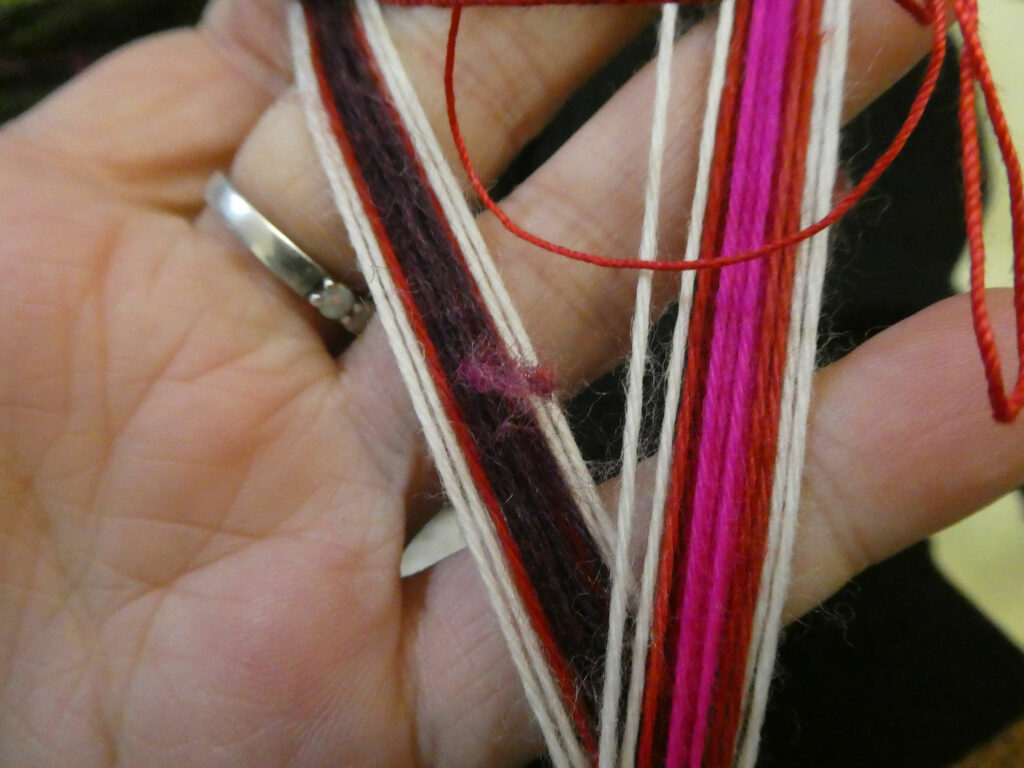
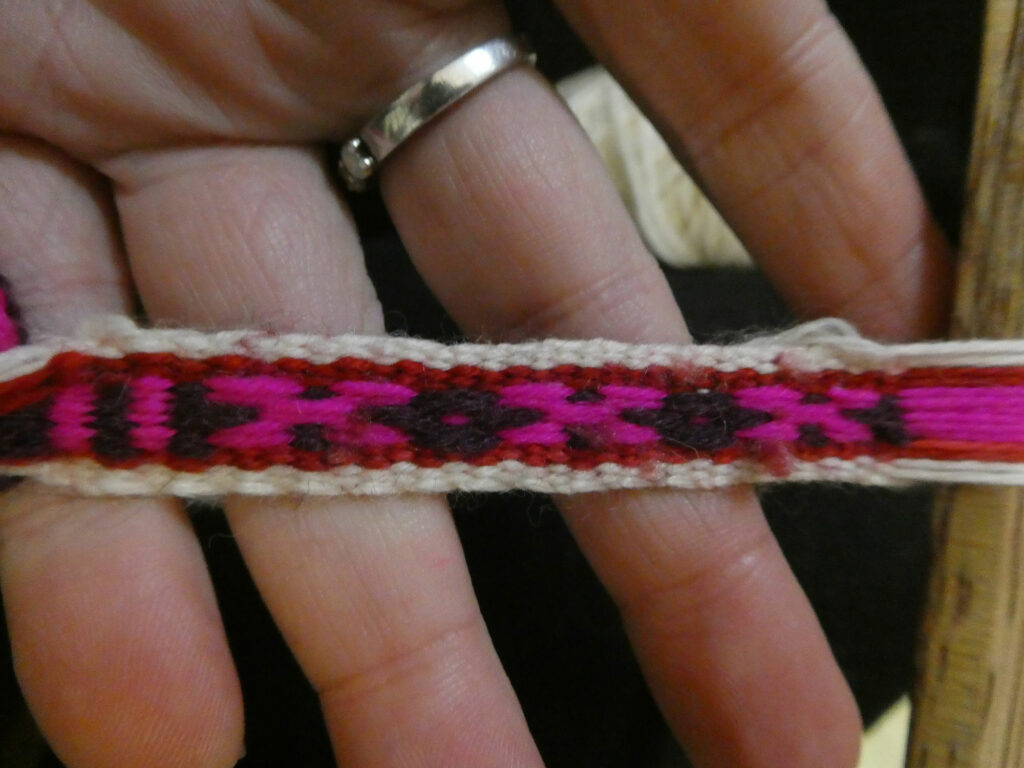
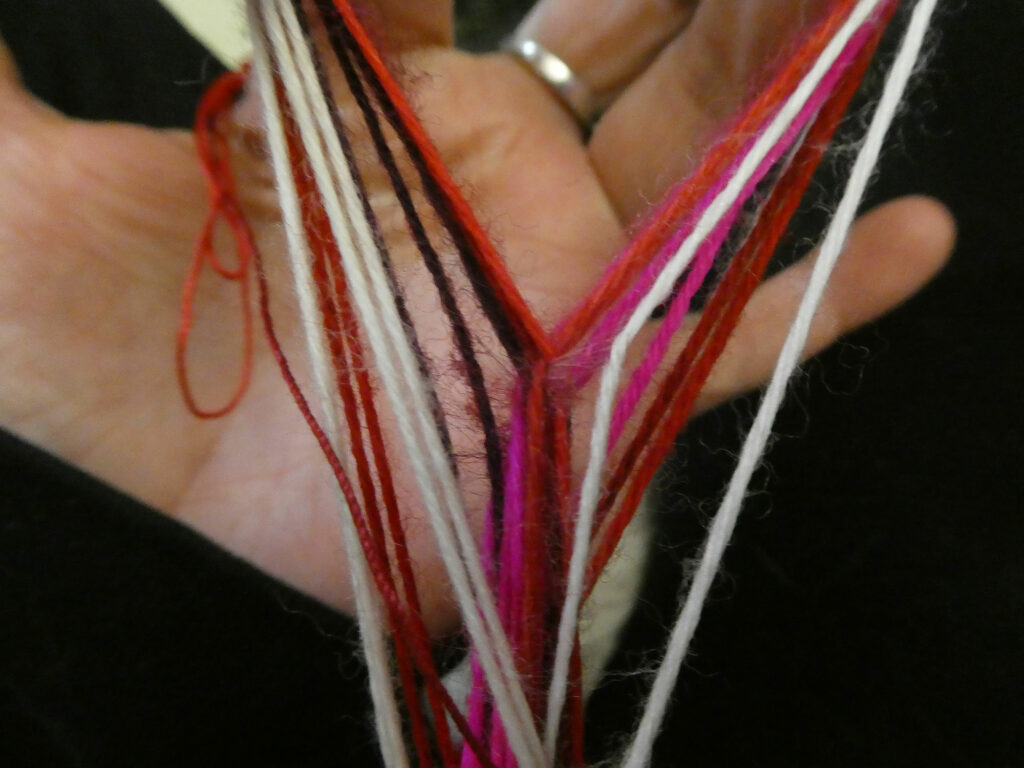
After a few more picks, the yarn was beginning to fuzz and shed, and lint was building up around the illawa and khallwa. The tension also felt strange, as the different yarns I used had different levels of stretch.
I managed a couple more pattern repeats than with the palette, but couldn’t have made a full band as there was just too much fuzz buildup, and the pattern didn’t even look that good.
Rating: 2/10
Yeoman Yarns Brittany 2 ply cotton.
This is the yarn I weave my teatowels out of, it comes in cones of 400g/3380m, and is a good budget price yarn for floor loom weaving. I’m sure results would be similar with most cotton weaving yarns.
Warping with this was difficult in the opposite way to the wool yarns; it had far less stretch than I was used to, so getting the knots lined up was hard in a different way. It’s also considerably finer than the wools, so would take a lot longer to weave a whole band from it.
While tying the illawa and getting started weaving, there was no fuzzing or shedding noticeable. However it didn’t feel right. The lack of elasticity meant that the small body movements I do to adjust my tension didn’t work in the same way as with wool, and it just wasn’t enjoyable to use.
I did manage a whole pattern repeat before stopping and thinking I would work on it another time, which I might, but I really didn’t like weaving with it, and I’m not convinced it’ll be strong enough to withstand weaving a whole band without a break.
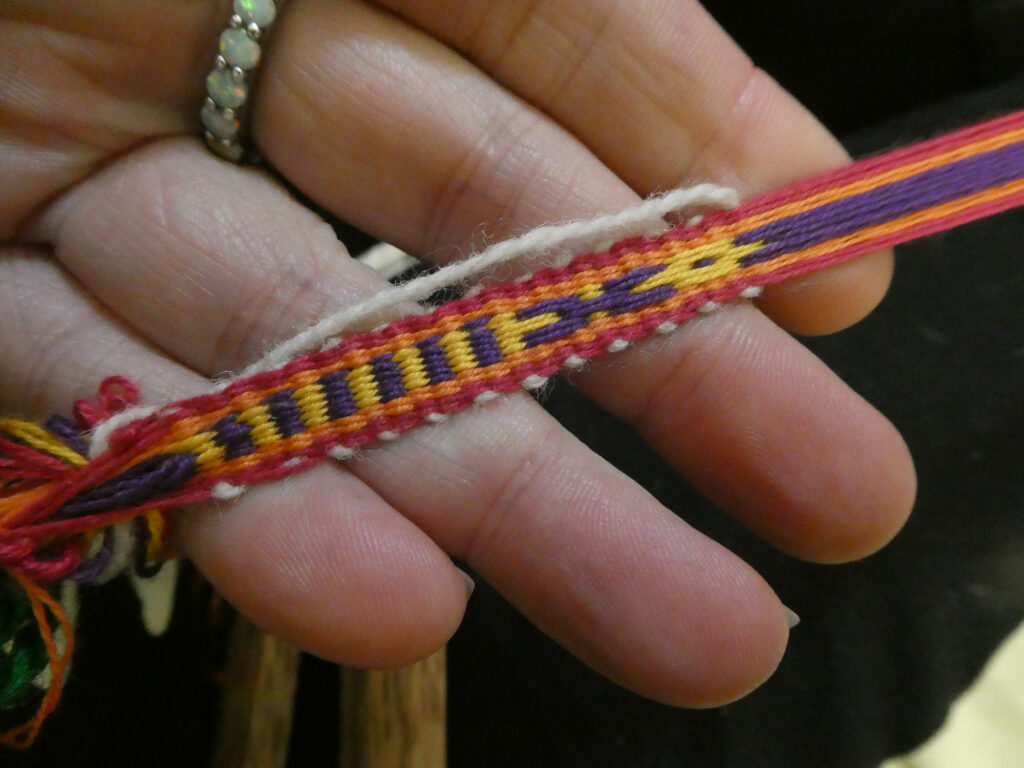
Rating: 3/10 No shedding or grabby threads to worry about, fairly good pattern definition, but just really not enjoyable to work with.
Now we move on to yarns with added twist. How much twist to add? Well, that is something you’ll need to decide for yourself. The less twist you add, the closer the yarns will be to the ones above, with lint and fluff sticking your threads together and making it hard to weave and your patterns not show up as well. The more you add, the harder it is to wrangle the yarn during warping, and the more the finished band biases.
Rowan Scottish Tweed 4 Ply
Once I’d added some twist, it was increasingly apparent that this is an incredibly unevenly spun yarn, with lots of slubby bits. The twist was collecting in the thinner areas making me concerned they would break, and not enough twist was getting to the thicker areas. I didn’t even bother trying to add this to a warp as it would have ended in tears.
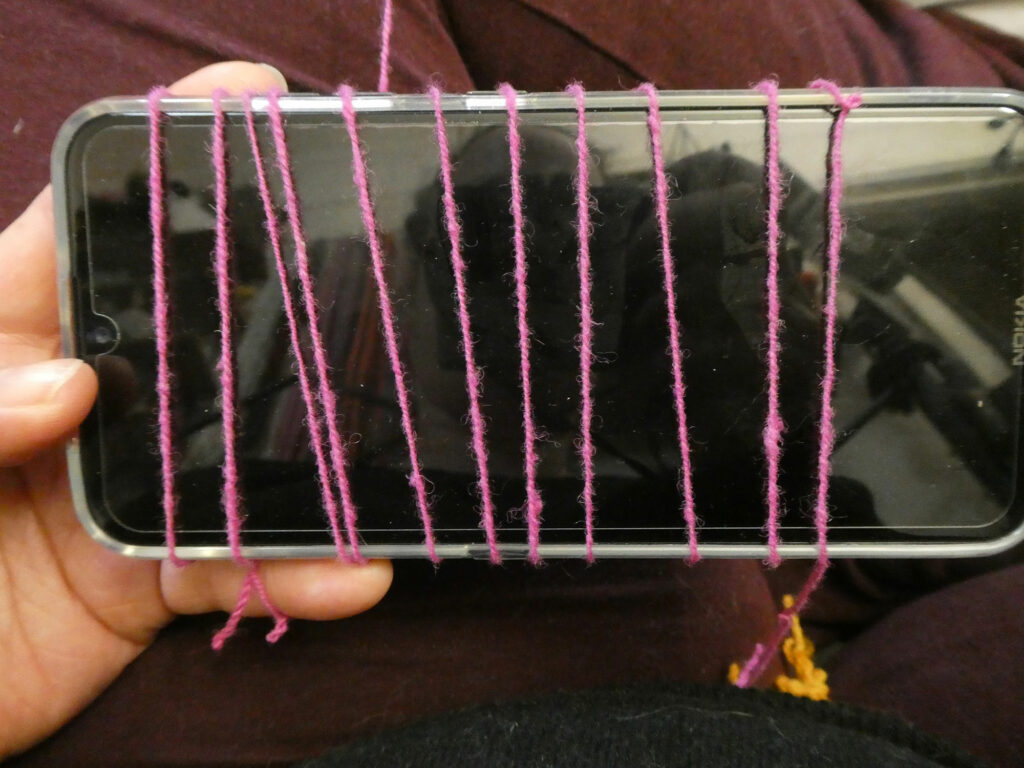
Rating: 0/10 Useless.
JaggerSpun Heather 3/8, Knitpicks Palette, Jamieson & Smith 2ply Jumper Weight
When twist is added, these yarns work out close enough to the same thickness that they work together, so I used them in the same warp so I could get the colours I wanted. They all have similar enough characteristics that grouping them together seems fair.
With a moderate amount of added twist the yarns are easy enough to manage during warping, and can manage a metre long band without fuzzing that stops the threads moving as they should, although there is a little buildup on the illawa by the end of the band. However the pattern definition isn’t great.
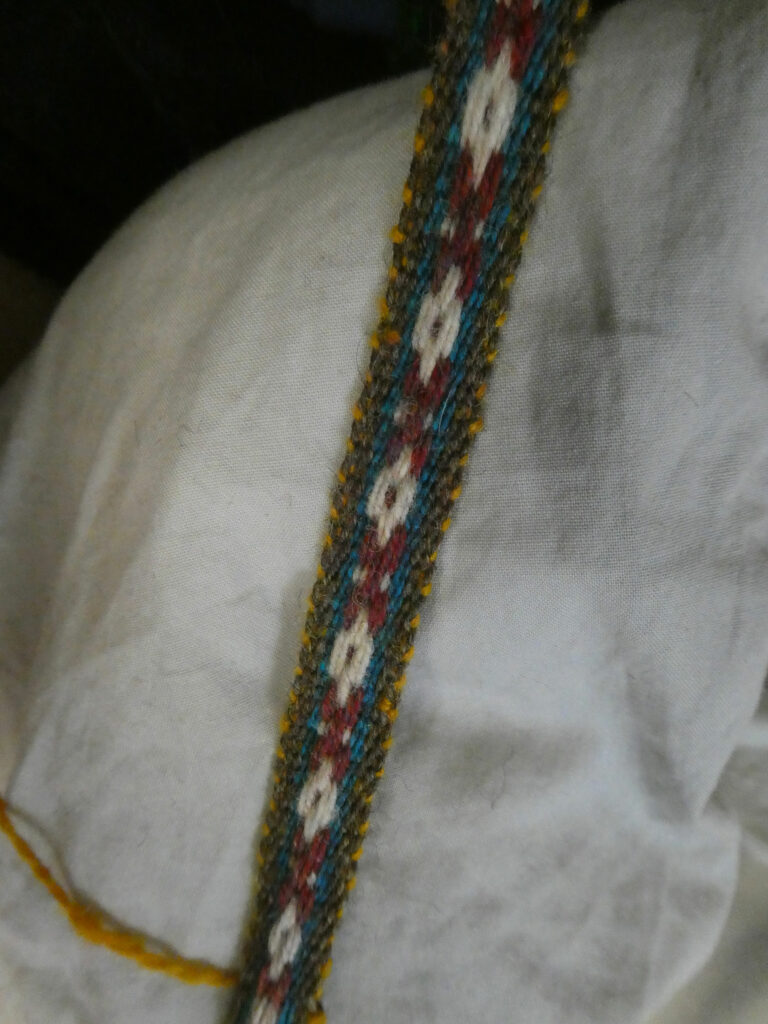
With higher added twist the yarns really want to twist back on themselves, so warping is a little more of a challenge, and the final band is fairly twisty, but the pattern is more distinct.
Rating: 6/10 Adequate
Harrisville Designs 2-ply Shetland
This is the yarn that fellow adjunct professor Cat uses for her beginner warps. It is similar to the yarns I tested above. I didn’t test warping with it as Cat sent me ready-wound warps, but on the weaving front it’s very similar, no problems with a clear shed but a little fuzz on the illawa by the end of the warp, and fairly good pattern definition.
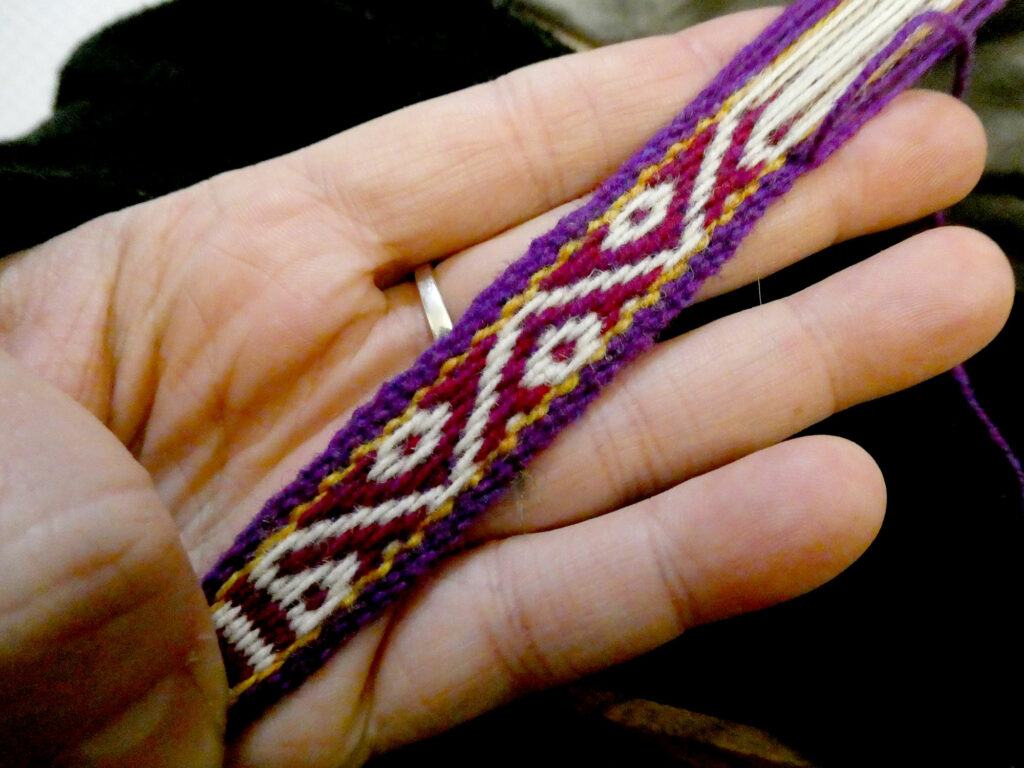
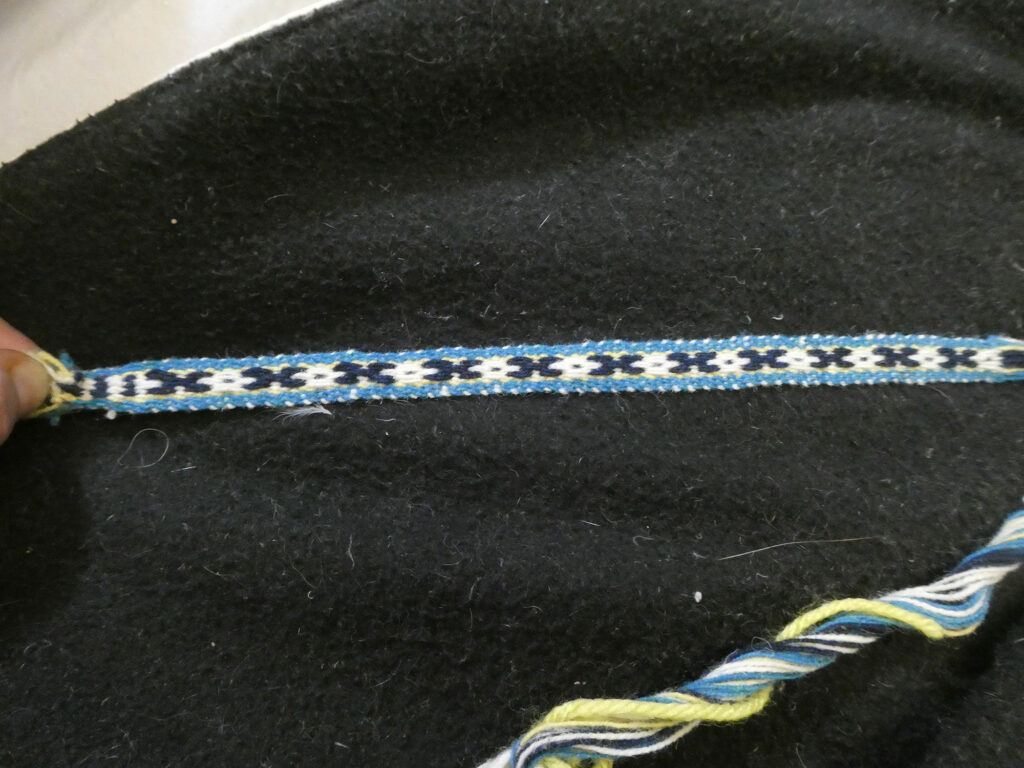
Rating: 7/10
Handspun
After trying the commercial yarns above and realising they weren’t as good as they could be, I began thinking ‘I wonder if I can buy a yarn that is a little finer, and has more singles twist, and…’ then realised that this is why I spin! When I want a yarn with certain characteristics, I make that yarn.
I made this video to show how I spin this sort of yarn on an espinner. I use a Daedalus Falcon, which is the fastest e-spinner on the market. If I didn’t have this, I’d rather do it on a spindle (ideally an Andean pushka, as unsurprisingly, the tools designed to make this sort of yarn do it best!) as using any other wheel would be very slow.
My first attempt at handspun didn’t have enough twist. It was easy to warp with, and was still high twist enough to not cause problems with the weaving, but the band hung limp and the pattern didn’t pop, although I am aware my colour choices didn’t help on this front.
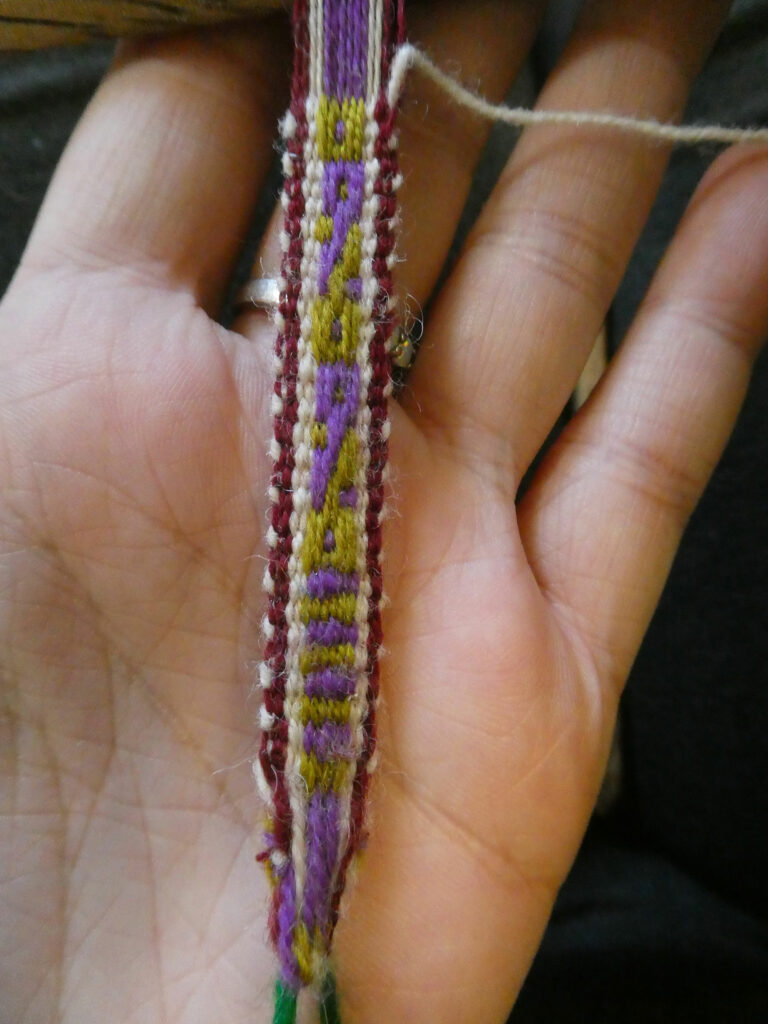
My second attempt had higher levels of twist, and the pattern showed better, but it still doesn’t have the very high twist angle of the andean yarns.
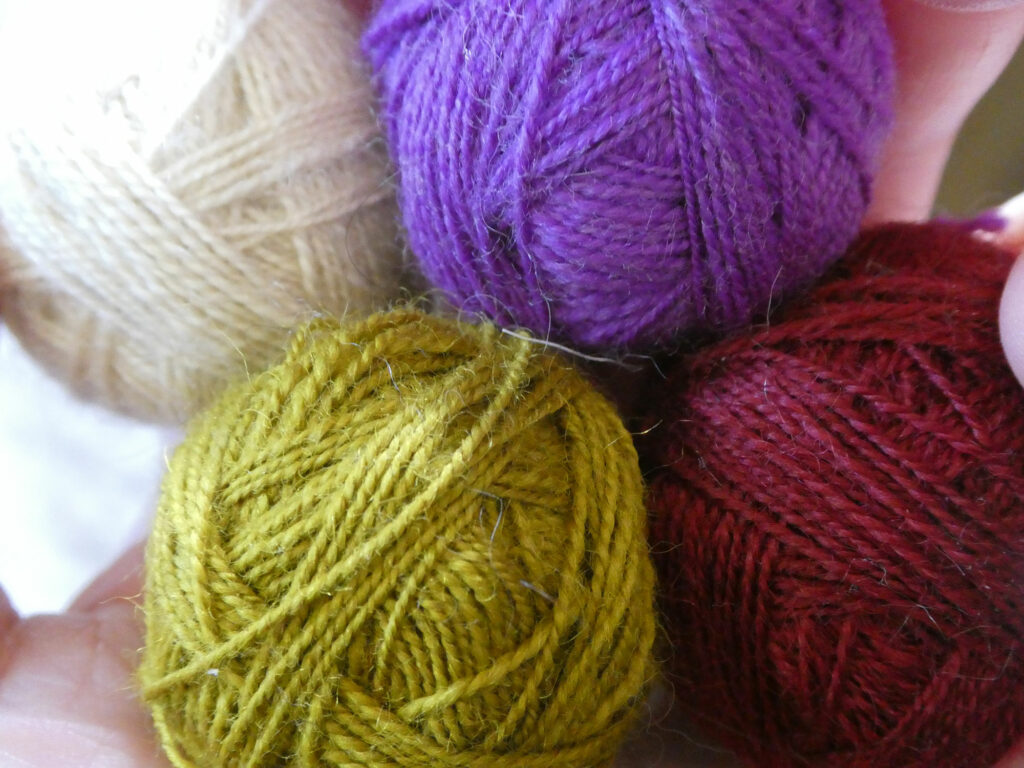
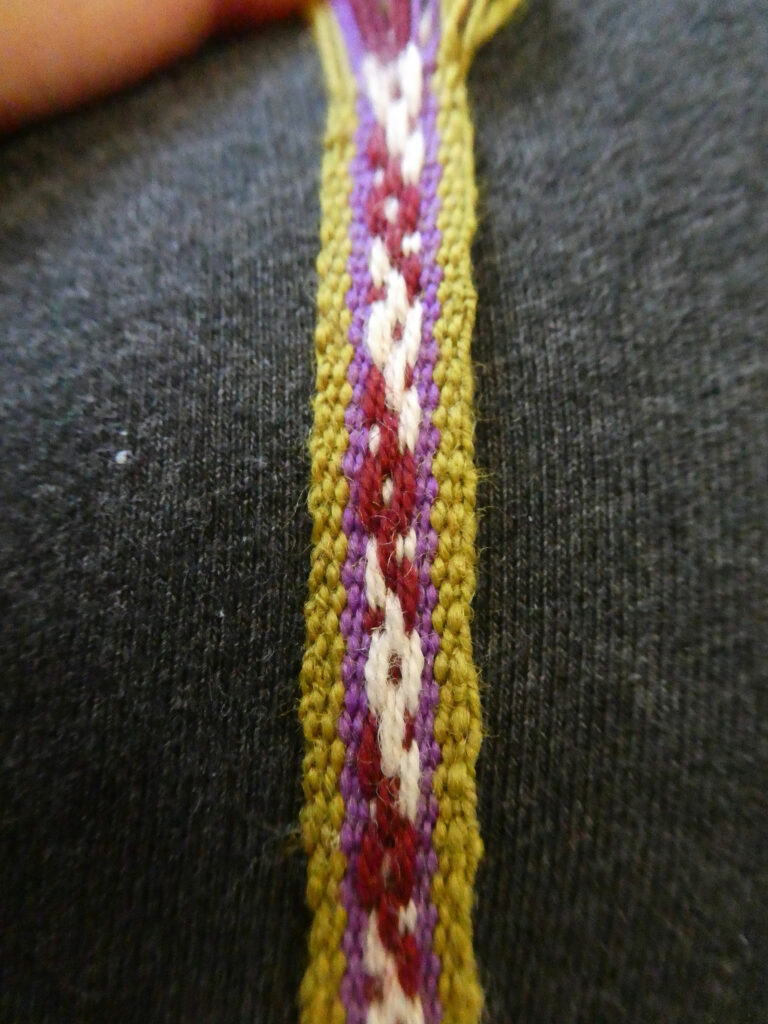
Finally I cracked it! These yarns were plied at a blistering 4200rpm, and I still couldn’t feed the yarn as fast as I’d have liked and needed to wait for twist to build. It’s totally worth it though, the patterns show up wonderfully and the yarn is a joy to weave with.
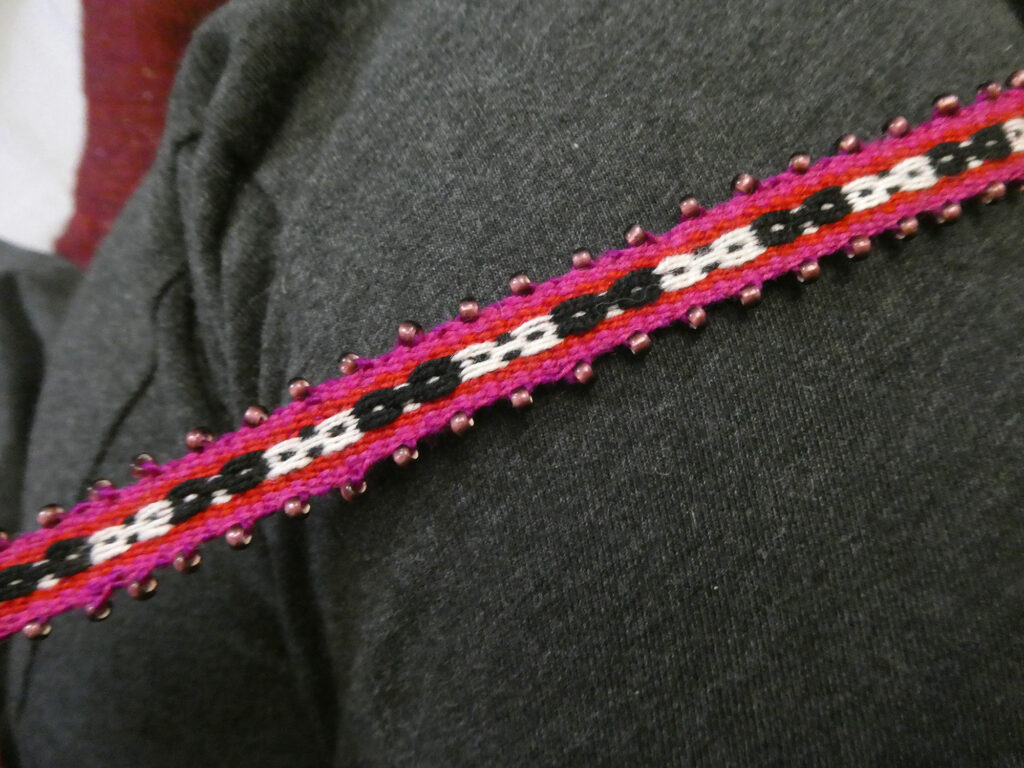
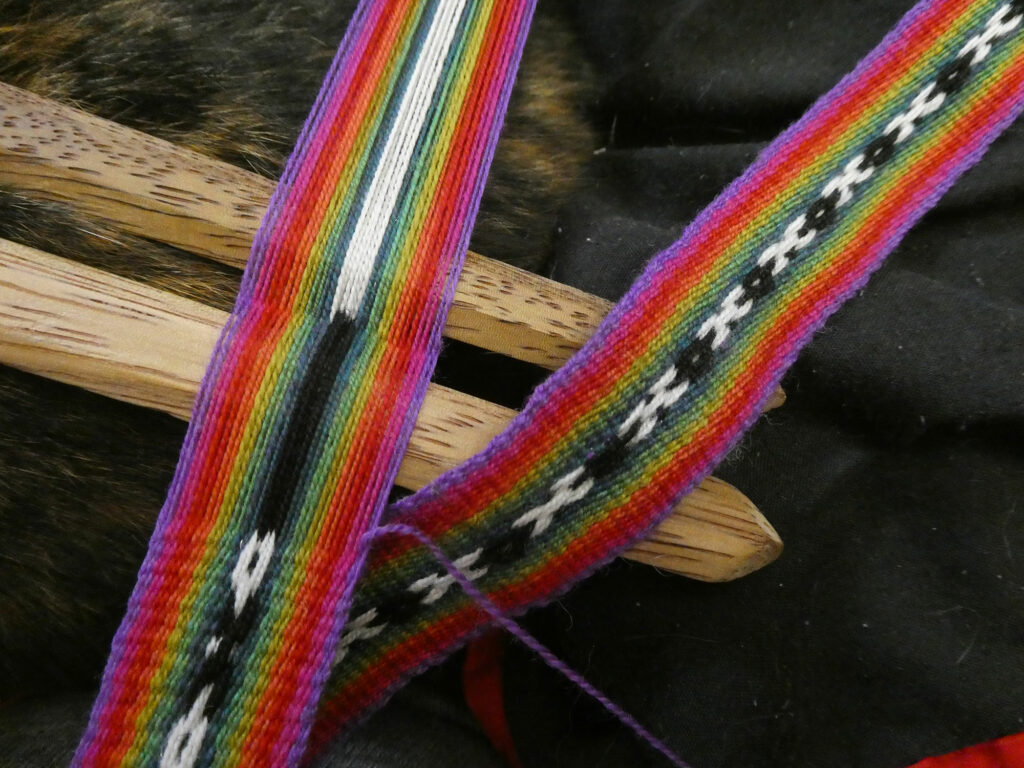
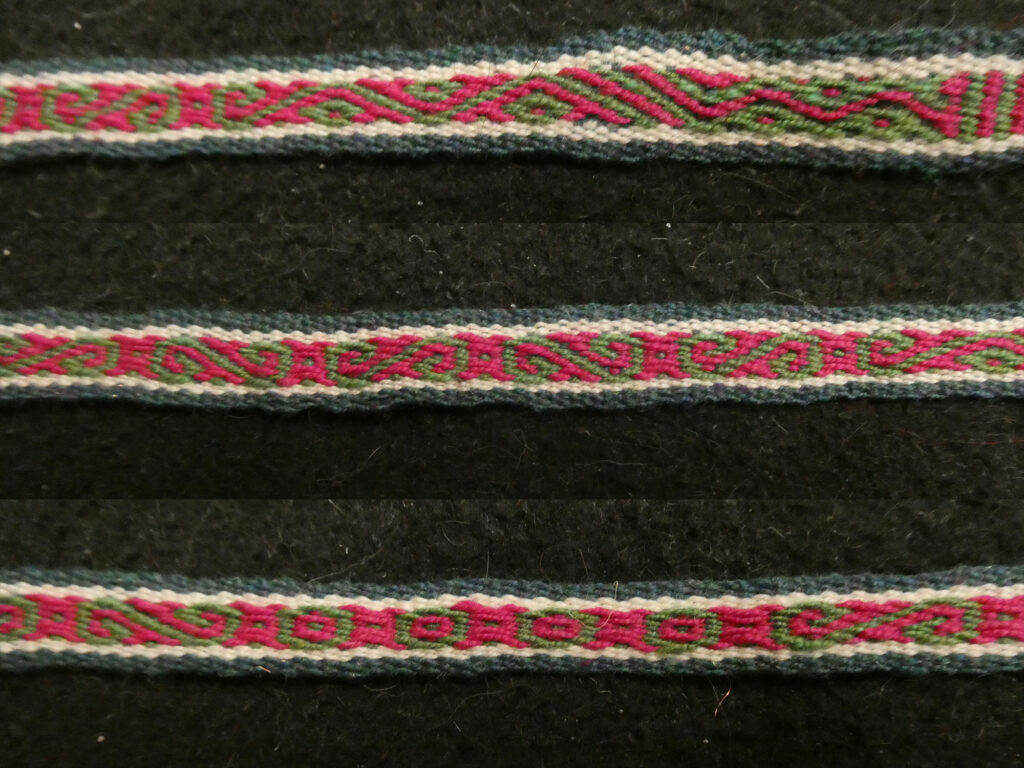
Rating: 8/10 – 10/10 Just being handspun doesn’t automatically make it perfect, but once you get the twist levels right, you’ll never want to weave with anything else.